Common Welding Mistakes and How to Avoid Them
Understanding Common Welding Mistakes
Welding is a highly skilled trade that requires precision, patience, and practice. However, even experienced welders can fall into the trap of making mistakes that compromise the integrity of their work. Whether you are a beginner or a seasoned professional, understanding common welding errors and how to avoid them can improve your results significantly.

Poor Preparation
One of the most frequent mistakes in welding is insufficient preparation of the materials. Failing to clean the base metals properly can lead to weld contamination, which weakens the joint. It's crucial to remove any rust, oil, paint, or dirt before beginning the welding process. This ensures a strong and clean weld with fewer defects.
Incorrect Electrode Selection
Choosing the wrong type of electrode for the metal being welded is another common mistake. Each electrode has specific properties and is designed for certain applications. Using an inappropriate electrode can lead to poor penetration and weak welds. Always refer to the manufacturer's recommendations to select the right electrode for your project.
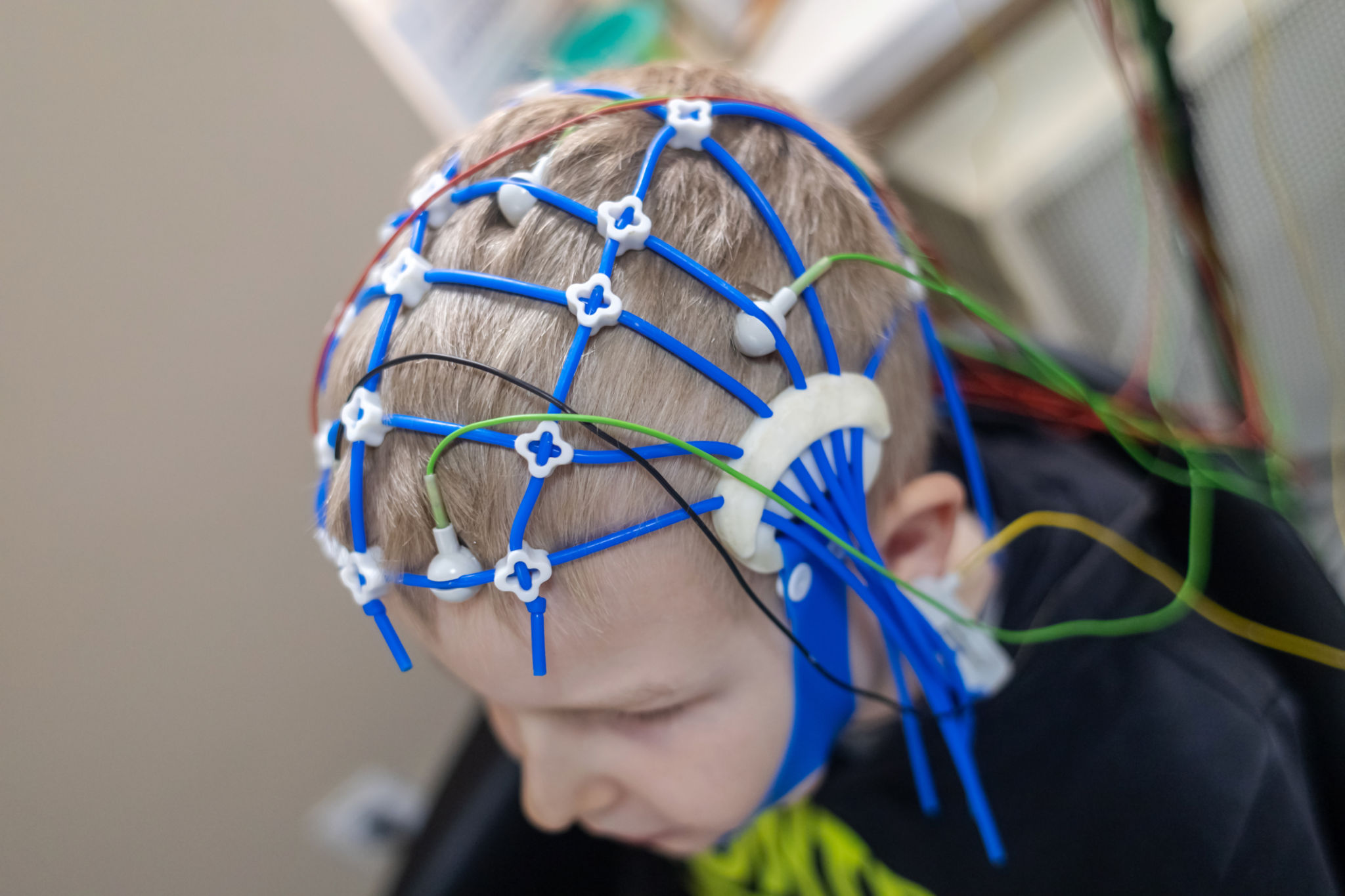
Techniques to Enhance Welding Quality
Inconsistent Travel Speed
Maintaining a consistent travel speed is essential for creating uniform welds. Moving too quickly can result in undercutting, while moving too slowly can cause excessive build-up and weak joints. Practice maintaining an even pace and adjust your speed according to the thickness of the materials being welded.
Improper Heat Settings
Setting the correct heat is vital for achieving strong welds. Too much heat can cause burn-through, while insufficient heat can lead to poor fusion. It's important to adjust the amperage settings based on the thickness of the material and the type of electrode being used. Test on scrap metal first to ensure the settings are correct.
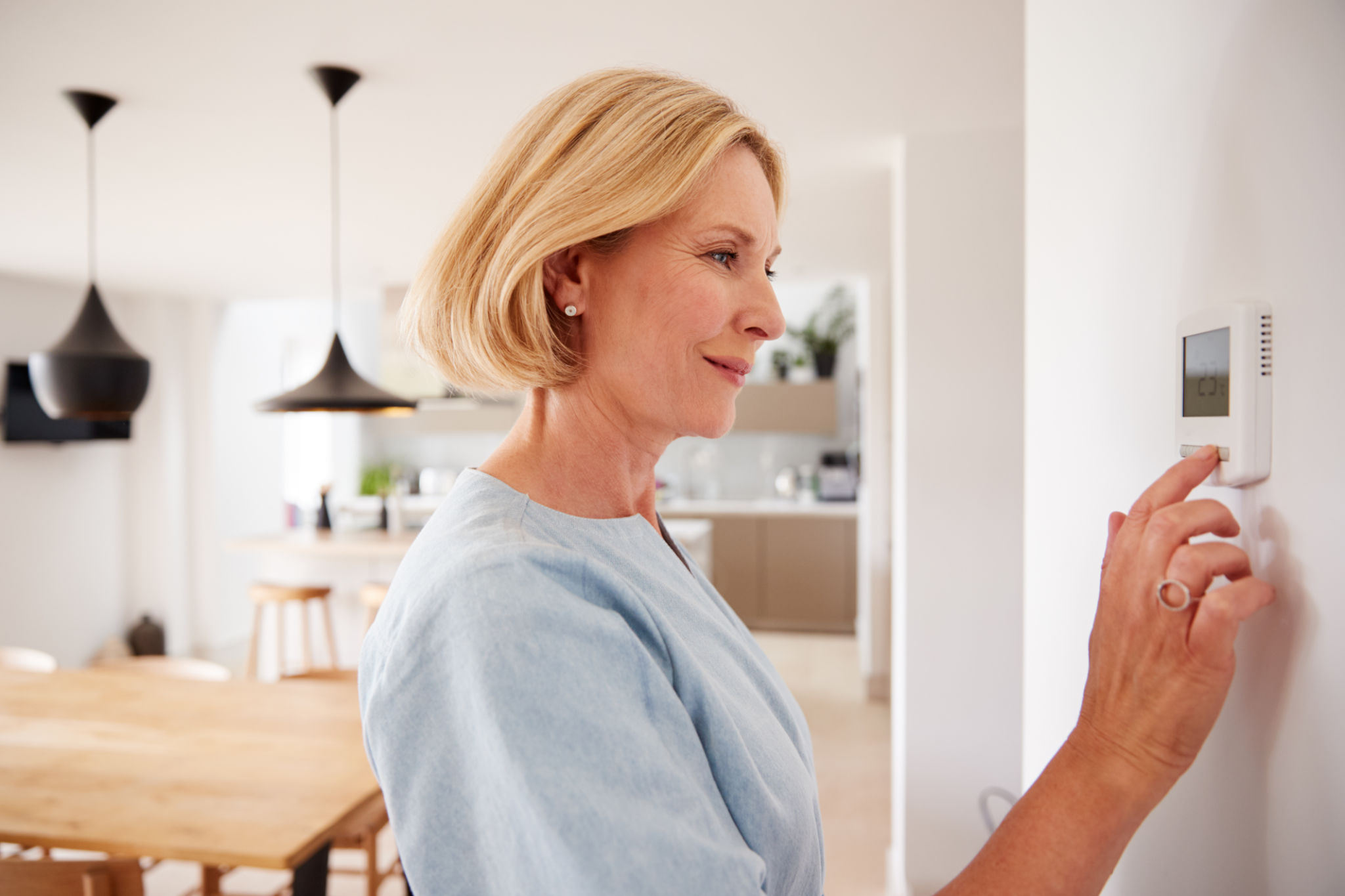
Avoiding Common Pitfalls
Lack of Safety Precautions
Ignoring safety measures is a serious mistake that can lead to injuries. Always wear appropriate protective gear such as gloves, helmets, and goggles. Ensure your workspace is well-ventilated to avoid inhaling harmful fumes, and keep fire extinguishers nearby in case of emergencies.
Poor Post-Weld Inspection
After completing a weld, it's crucial to conduct a thorough inspection. Overlooking this step can result in unnoticed defects that may compromise the structure's safety and longevity. Check for cracks, porosity, and other imperfections that might require rework.
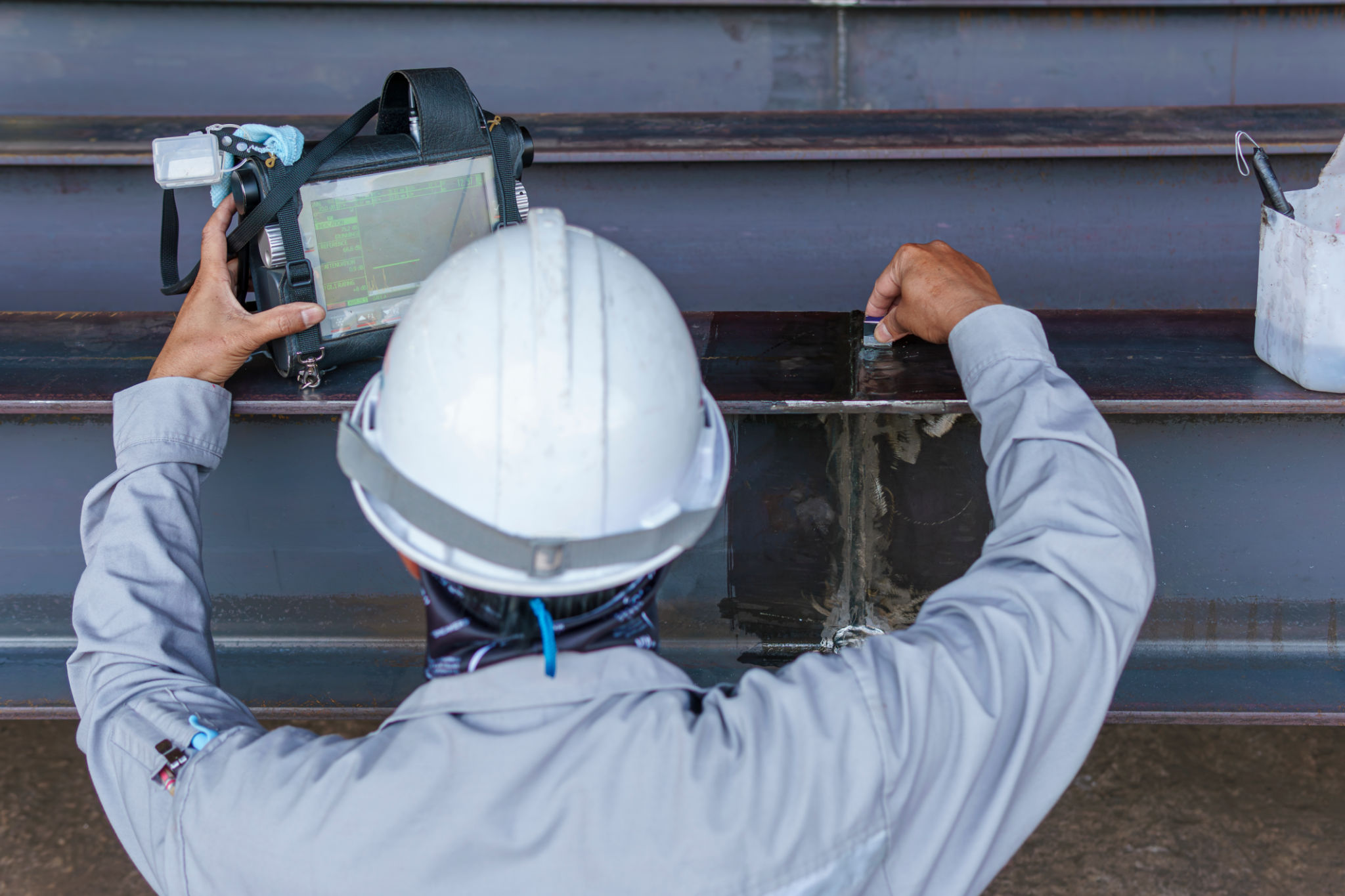
Conclusion
Avoiding common welding mistakes requires vigilance and practice. By focusing on proper preparation, selecting the right materials and techniques, and adhering to safety protocols, you can create high-quality welds that stand the test of time. Remember that continuous learning and improvement are key components of mastering the art of welding.